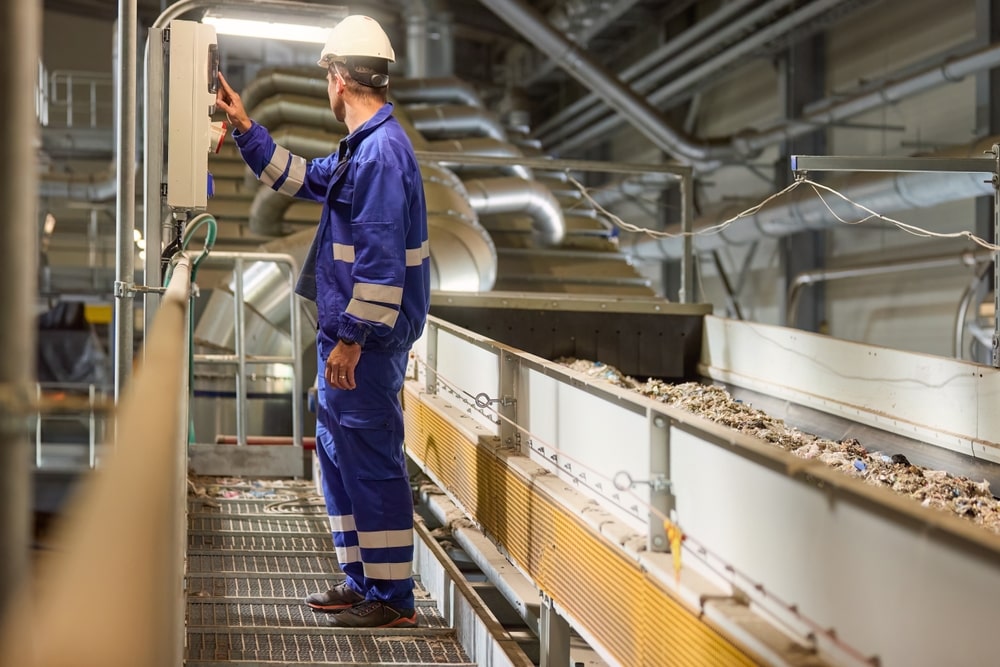
Understanding how conveyor belt tracking works and why it’s important is essential for anyone who depends on a belt to keep their operations running smoothly and efficiently. Continue reading to discover helpful conveyor belt tracking tips and learn how to adjust a conveyor belt in three simple steps.
Conveyor Belt Tracking Tips
Mistracking is one of the most common problems for any business using a conveyor belt. A variety of factors can negatively affect conveyor belt tracking, some of these include:
- Structure and pulley misalignment
- Incorrect splicing procedure
- Poorly manufactured belt
- Overtensioning of the belt
Pinpointing the root cause of mistracking is essential if you want to learn how to adjust a conveyor belt to run straight and extend the life of your belt.
Below, we’ve provided some helpful tips to look out for if you suspect a belt tracking problem.
1. Make Sure The Conveyor Frame Is Level & Square
Sometimes with tracking issues, the belt itself isn’t the problem. If a conveyor bed isn’t properly level or square, it will cause the belt to move to one side or the other. Fortunately, checking both these is fairly simple and can be done using a standard-level tool. Examine the frame and pulleys to ensure the structure is “true” (relative to the center line) and level (side to side).
2. Confirm The End Pulleys Are Square
All pulleys, snub rollers, carrying idlers, and return idlers must be square with the frame (perpendicular to the belt center line) and parallel to each other. You can check this by measuring the diagonals. Check the dimensions from one corner to the opposite corner on each side of the conveyor. The final measurements should equal one another.
3. Check For Any Debris In Your System
Cleanliness is key when it comes to proper belt tracking. It’s fairly common to find foreign matter or common debris building up at one or both of the end pulleys. When this happens, it’s essential to clear the buildup otherwise it may create a crown or raised portion on the pulley which results in belt mistracking. Knowing how to properly clean and maintain your conveyor belt will help ensure debris buildup doesn’t become a problem.
4. Ensure Your Conveyor Belt Is Cut Straight
If a conveyor belt is manufactured, slit, and spliced properly, it will move where it’s directed. However, if there are flaws in belt manufacturing or the belts aren’t cut or spliced correctly belt tracking issues can occur. If you suspect your belt wasn’t cut properly, you can remove it from the frame and lay it out on the floor to ensure it’s straight.
5. Check The Belt Tension
Overly loose or tight belts can cause an assortment of problems, mistracking being one of the most common. Follow the guidelines from your belt supplier to find the proper amount of tension to apply.
How To Track A Conveyor Belt
Conveyor belts are influenced by gravity and friction. It’s essential to understand these forces and how pulleys work, in order to control the belt’s path. The key to conveyor belt tracking is to keep everything level, use the pulleys effectively, and ensure proper alignment.
1. Understanding How the Belt Moves
The first thing to consider when tracking a conveyor belt is gravity and how it influences the belt’s movements. A conveyor belt naturally wants to follow the lowest point. If any part of the conveyor isn’t perfectly level, the belt will pull towards that lower side. This is why it’s important to keep everything as flat as possible.
2. Controlling the Belt
The second factor to consider for conveyor belt tracking is friction. We use friction to control where the belt goes. This is where the pulleys on the conveyor play a key role. The more the belt touches a pulley (more wrap), and the bigger the pulley, the more control it has over the belt.
Essentially, this means the belt tries to go straight out from the pulley. To keep the belt centered, it’s usually best to adjust only one or two pulleys while keeping the others fixed. However, on long conveyors, you might need to adjust more.
It’s also important to keep in mind that there are limits to control when making belt adjustments. You can only steer a belt as much as it can bend. This means that belts with more lateral stiffness will resist direction changes more than those that are flexible. If you try to force the limits of a belt, it can start to move in the opposite direction, resulting in deformation of the belt and making it uncontrollable.
3. Aligning Equipment
Proper alignment and roller maintenance are crucial for a smoothly running conveyor system. Even small alignment errors can cause big problems on a conveyor. A few rollers slightly out of line can create more issues than one roller that’s very out of line.
It’s important to check and adjust roller positions often. Taking shortcuts by just measuring from one roller to the next can lead to even bigger problems later on. Broken or stuck rollers can also cause major issues. These are often hard to see, especially the ones at the back of the conveyor. Remember, always check for damaged rollers before installing a new belt.
Conveyor Belt Adjustment Rules & Procedures
After learning how conveyor belt tracking works, it’s important to know a few basic rules to follow when making adjustments. These will ensure no further damage is done to the belt and the process is completed successfully.
- Focus on the return run first, adjusting it towards the tail pulley. Once that’s done, work on the top run in the direction the belt moves. Begin with an empty belt. After checking the alignment, fully load the belt and check the alignment again.
- Always adjust the belt’s tracking while the conveyor is running. Make these adjustments along a section of the conveyor before the problem area.
- Let the belt run for several minutes, or at least three complete rotations after adjusting an idler to see if further adjustments need to be made. If you’ve overcorrected, simply readjust the same idler back to its original position instead of changing other idlers or rollers.
When designing a procedure for conveyor belt tracking, we recommend considering the following:
- Avoid turning constants into variables. When everything is known to be square and level, index the rollers. Sometimes simple, well-thought-out marks on the equipment can prevent hours of frustration.
- Guide the belt with the tracking rollers and leave the others alone. The tracking provisions were designed to control a stable system. If they are unable to control the belt, the system isn’t stable and something is broken.
- Avoid excessive adjustments by establishing a disciplined belt tracking procedure based on observations at fixed intervals and try not to make gross adjustments if possible.
- Limit the number of personnel associated with tracking a specific belt and/or keep a log to prevent erroneous adjustments.
Remember, every belt is different, so while these guidelines are helpful to keep in mind when making conveyor belt tracking adjustments, the best thing to do if you have questions or concerns is to contact a repair or replacement specialist who can help you navigate the situation.
Do you have questions about a belt repair or replacement? Talk to us today to see how we can help.